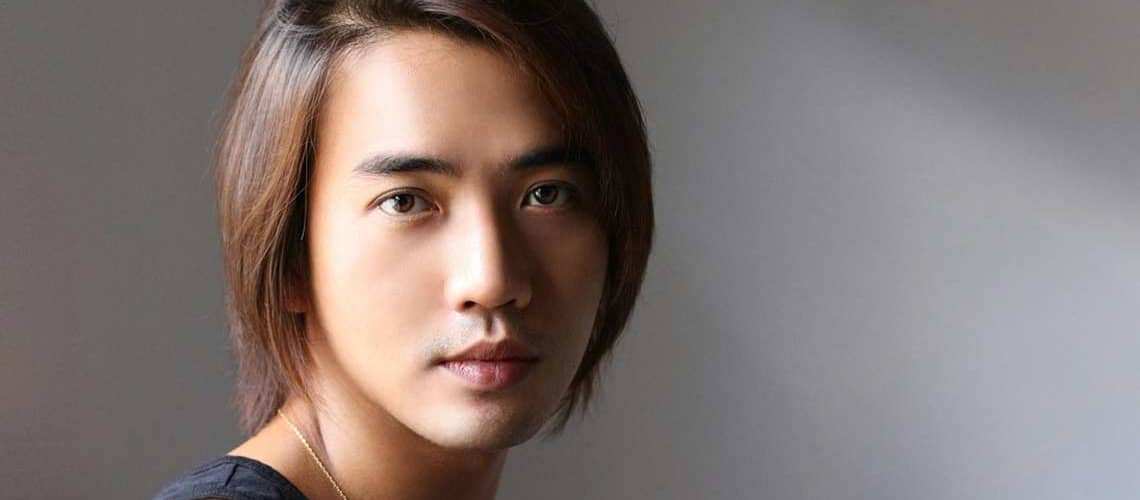
Most people think of 3D printing as a prototyping technology rather than a production technology. That is, they would never think to use it for making large batches of end use parts. And most of the time they’d be completely right.
However, there are some interesting circumstances when the most common and cost effective method of 3d printing (fused deposition modelling) is actually the best choice of production technology.
Of the dozen common methods of plastic manufacturing, 3d printing offers its own unique set of advantages and disadvantages.
3D printing favors customization and is excellent for small quantity batches. It allows you to make parts with as much variety and complexity as you want at no additional cost. It allows you the flexibility of changing a product after production has started, also at no extra cost.
On the downside 3D printing can’t offer any economies of scale. It is essentially no cheaper on a per- unit basis to make a large batch of parts than it is to make one.
For true high volume production you need a process like injection molding, which favors repetition and standardization. For a visual aid I borrowed this graph from the book ‘Makers: The New Industrial Revolution’ by Chris Anderson. It uses plastic ducks to illustrate the strengths and weaknesses of injection molding vs 3d printing in volume.
Credits: All content taken from www.3dprinting.com